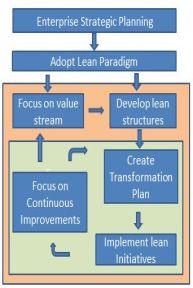
Transition to Lean Enterprise
At the core of Lean Thinking is the relentless elimination of waste which it defines as any activity that does not add value. When implemented properly, spectacular improvements in efficiency and effectiveness along with associated reductions in leadtime and resources required can be achieved. The first step in the application of Lean Thinking is to correctly identify the value produced from your customer’s point of view, followed by a mapping exercise of all the end to end linked actions that transform inputs into outputs. This is the ‘Value Stream Map’ which will help identify non value adding steps or waste. Having eliminated or reduced the waste, the next phase is to line up all the remaining steps so that the value flows continuously, then let the customer pull value by only producing what the customer demands. Pursue perfection by improving the value definition, redefining the value stream and more vigorously eliminating waste. There are a myriad of tools and techniques such as KanBan, SMED, JIT etc. which can help in the achievement of a lean organisation but the implementation of a few or even many of these techniques is unlikely to yield positive results unless carried out as a part of an overarching process with committed knowledgeable and resourced champions at the helm. Niallo Carroll can help create this process in your organisation and with funding from the Enterprise Irelands Lean Start programme it is a very cost effective way to start your journey to lean.
Enterprise Transformation
Having successfully implemented Lean Thinking on a focused area in an organisation. It is time to think of ‘Lean Enterprise Transformation’. Just as the application of a few “Lean Tools” does not make a Lean Process, the application of Lean Thinking to a few processes does not make a Lean organisation. A broader approach is required. The interdependencies of processes need to be determined and improvement plans need to extend throughout the organization to all departments and beyond, such as to suppliers and partners. The needs of the customer need to be fully understood and the point of view of all other stakeholders who could be affected by or affect the organisation are considered. Although Lean Thinking has its roots in manufacturing, much of the benefits of Lean have been realised through its application to supply chain management, customer service, distribution and other non-manufacturing related processes. Lean can be applied to any process where improved performance and reduced waste is desired. Niallo Carroll can systematically guide your organisation through the evaluation, planning and execution cycles of a lean transformation programme and help develop the infrastructure to sustain lean in your organisation in the long term.